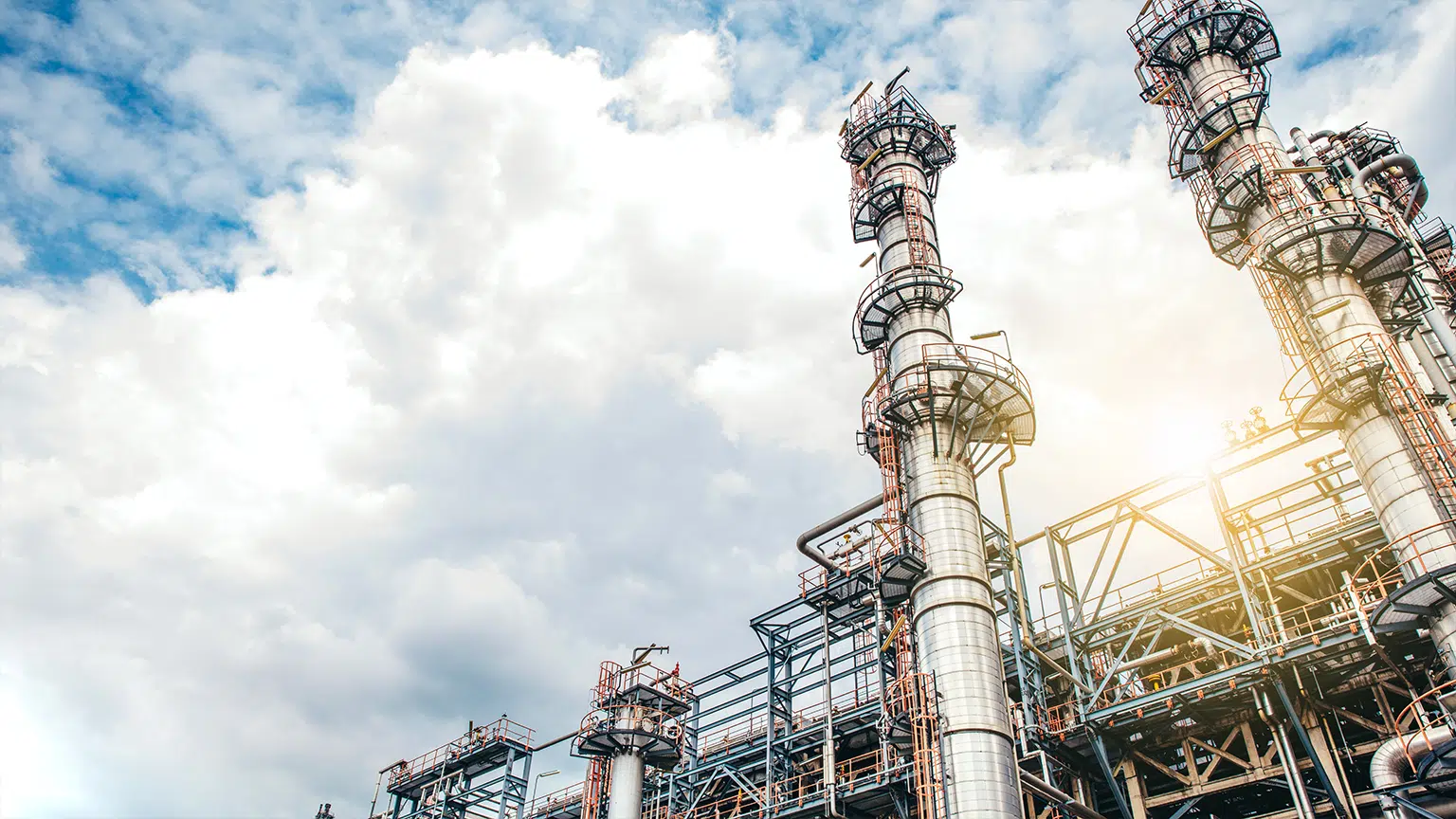
Gas detection in the Manufacturing Industry
Gas detection in the Manufacturing Industry – Manufacturing is the production of finished goods using tools, human labour, machinery, and chemical processes. Manufacturing enables businesses to sell finished products at a higher price than the raw materials’ cost. Large-scale manufacturing facilitates mass production through assembly line processes and advanced technologies. Efficient manufacturing techniques allow companies to benefit from economies of scale, producing more units at a reduced cost. Manufacturing is the process of converting raw materials or parts into finished goods using tools, human labour, machinery, and chemical processes. Before the Industrial Revolution, most products were handmade using human labour and basic tools. The Industrial Revolution introduced mass production, assembly line manufacturing, and mechanisation, allowing for larger quantities of goods to be produced at a lower cost. Manufacturing can be defined and categorised by different types, processes, or techniques.
Understanding Manufacturing
Manufacturing is a critical part of the economy, involving the processing and refining of raw materials like ore, wood, and foodstuffs into finished products such as metal goods, furniture, and processed foods. This transformation adds value to the raw materials, increasing the price of finished products and making manufacturing a highly profitable segment of the business chain. Some individuals specialise in the skills needed for manufacturing, while others provide the necessary funding for tools and materials. As mentioned, manufacturing efficiency can lead to higher productivity and cost savings.
Manufacturers achieve this by:
– Reducing redundancies
– Improving work quality
– Updating equipment and procedures
– Setting realistic goals
– Streamlining intake, supply chain, and distribution channels
Types of Manufacturing
The methods of manufacturing products have evolved over time. Traditionally, goods were produced using raw materials, and in some cases, they still are. Hand manufacturing, which involves using basic tools through traditional processes, is often associated with decorative art, textile production, leatherwork, carpentry, and certain types of metalwork. Handmade goods are labour-intensive and time-consuming. Depending on the supplier and the type of goods, these items can sometimes command a high price. For example, unique handmade fashion items can be sold at a premium compared to mass-produced products. However, there are instances where artisans using these techniques may face exploitation, particularly in regions with lax labour laws and high job demand. Larger businesses utilise mechanisation to mass-produce items on a much larger scale. This process involves the use of machines, reducing the need for manual manipulation of materials. While minimal human labour is required for production, highly skilled individuals are often needed to operate and maintain the machinery.
Gas detection in the Manufacturing Industry
In manufacturing environments, gas detectors are essential for maintaining safety and compliance with health regulations. These devices are used to monitor the presence of hazardous gases, providing early warnings to prevent accidents and health hazards specific to manufacturing processes.
Enhancing Worker Safety
Gas detectors can identify the presence of harmful gases like carbon monoxide, hydrogen sulfide, ammonia, and chlorine, which can pose significant health risks to workers. Early detection allows for immediate evacuation and medical attention, preventing serious health issues.
Gas detection in the Manufacturing Industry – Regulatory Compliance
Gas detectors help manufacturing plants comply with OSHA regulations by ensuring that gas levels remain within safe limits, thereby avoiding fines and legal issues. Detecting and controlling gas emissions helps plants comply with environmental regulations, minimising the impact on the environment and avoiding penalties. Certain gases can be corrosive and damage equipment and infrastructure over time. By detecting these gases early, maintenance can be performed proactively to prevent costly repairs and downtime. Early detection of gas leaks prevents damage to equipment and reduces the risk of production halts, ensuring smooth and uninterrupted operations.
Gas detectors provide real-time data on gas levels, allowing for immediate response to any deviations from normal levels. This proactive approach minimises downtime and keeps production processes running smoothly. Monitoring gas levels helps optimize the use of ventilation systems, ensuring that they are activated only when necessary. This can lead to energy savings and reduced operational costs.
Data Logging and Analysis
Gas detectors can log data over time, allowing for the analysis of trends and identification of potential problem areas. This data-driven approach can lead to improvements in safety protocols and operational processes. In the event of an incident, data from gas detectors can be used to investigate the cause, helping to prevent future occurrences and improve safety measures.
To view the full guide and recommended products, download the guide below!