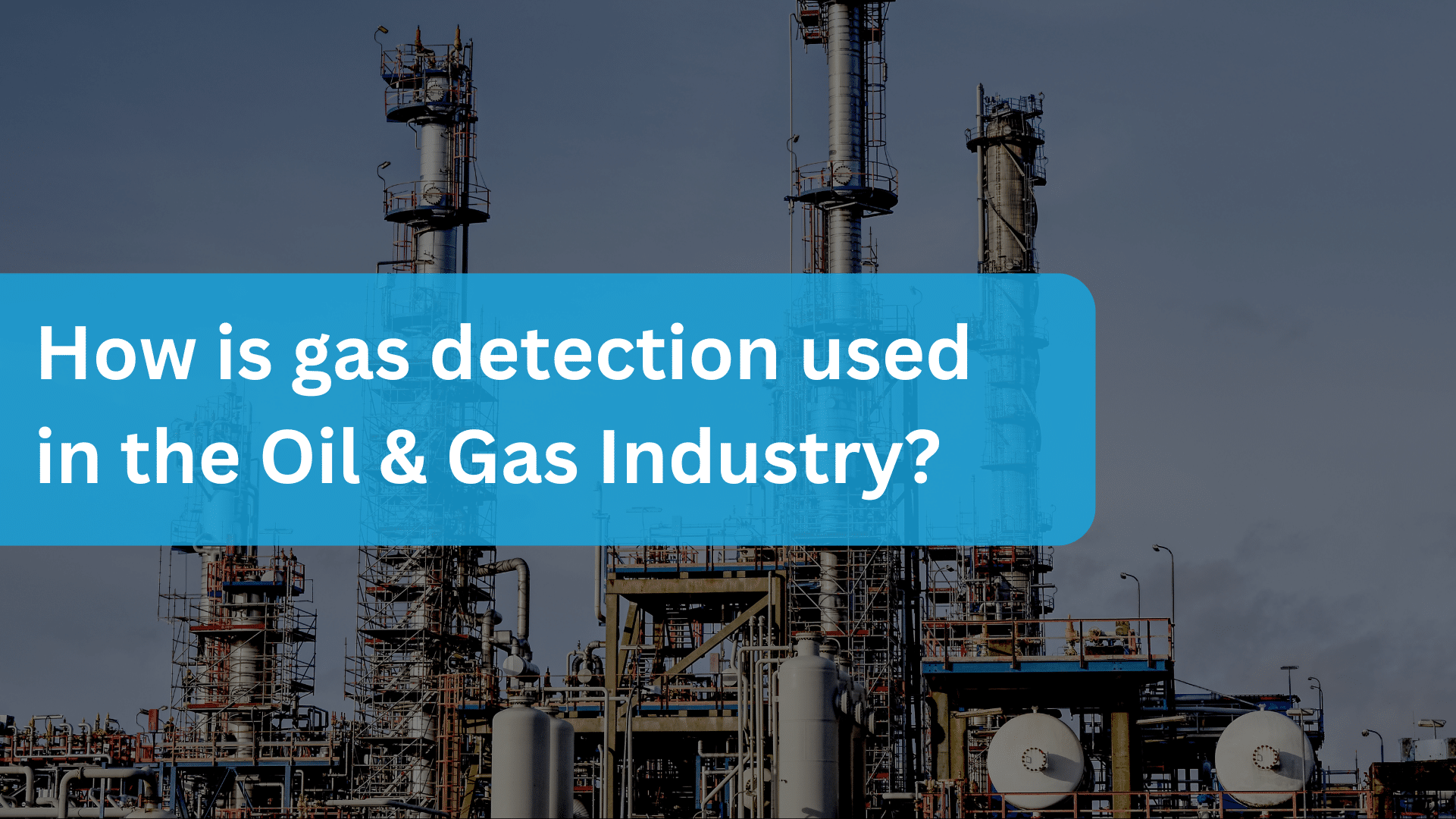
UK Oil & Gas Refineries
Petroleum refining in the United Kingdom produced approximately 51.45 million tonnes of petroleum products in 2023, reflecting a 16% decline from 2015 and a 32% decrease from 2011. The UK’s downstream oil industry includes six major refineries and one smaller facility.
The key operational refineries and their capacities are as follows:
- Phillips 66 – Humber Refinery (South Killingholme): 221,000 barrels per day
- Prax – Lindsey Oil Refinery (North Killingholme): 111,300 barrels per day
- Petroineos – Grangemouth Refinery: 150,000 barrels per day
- Essar Energy – Stanlow Refinery: 190,000 barrels per day
- Valero Energy – Pembroke Refinery: 270,000 barrels per day
- ExxonMobil – Fawley Refinery: 270,000 barrels per day
- Haltermann Carless – Harwich Refinery: 0.5 million tonnes per year (approximately 10,500 barrels per day)
The total operational refining capacity across these sites is approximately 1,222,800 barrels per day, equivalent to around 58 million tonnes per year.
The Process
Fractional distillation is a key process in oil and gas refineries because it separates crude oil into useful parts called fractions. Crude oil is a complex mix of hydrocarbons, and since each hydrocarbon has a different boiling point, the process divides them based on temperature. As a result, it produces gases, petrol, diesel, and heavy lubricating oils, each with important industrial uses.
The process takes place in a tall fractionating column, which contains multiple trays and condensers at different heights. First, crude oil is heated in a furnace to around 350–400°C. Due to this intense heat, the crude oil turns into vapour. Next, these vapours enter the column, where temperatures gradually decrease from the bottom to the top.
Different hydrocarbons condense at different temperatures. As vapours rise through the column, separation occurs naturally. Specifically, heavy hydrocarbons, like bitumen and heavy fuel oils, have high boiling points and condense near the bottom, where it is hottest. In contrast, lighter hydrocarbons, which have lower boiling points, rise higher before condensing. Consequently, this allows different fractions to be collected at various levels.
At the top, the lightest hydrocarbons—methane, ethane, propane, and butane—remain as gases. These are commonly used for liquefied petroleum gas (LPG) or petrochemical production. Moving slightly lower, petrol (gasoline) condenses and is primarily used for motor vehicles. Below that, naphtha is collected for chemical production and petrol blending. Furthermore, kerosene, which is essential for aviation and heating, condenses next, followed by diesel and gas oil, both crucial for transport and industry. Finally, the heaviest fractions, such as lubricating oils, fuel oil, and bitumen, settle at the bottom and are used for ship fuel, road surfacing, and industrial lubricants.
Overall, fractional distillation is essential in refining crude oil. Without it, crude oil would be too complex to use effectively. However, additional processes like cracking and reforming further improve product quality. Ultimately, this refining process ensures that industries, transportation, and daily life have the necessary fuels and materials.
In addition, gas detection plays a crucial role in oil refineries during fractional distillation. Since handling volatile hydrocarbons at different temperatures and pressures increases the risk of gas leaks, fires, and toxic emissions, monitoring is essential. To address this, fixed gas detectors are strategically placed throughout the distillation unit to track gases like methane, propane, and butane at the top, as well as heavier vapours like naphtha and kerosene at lower levels. As a result, these detectors help prevent fires and explosions, ensure safety compliance, and protect workers and equipment. Furthermore, portable gas detectors allow staff to check for gas leaks during maintenance and operations. By implementing gas detection systems, refineries can operate both safely and efficiently.
Cracking
Crude oil contains hydrocarbons that don’t always match market demand. In fact, many are large molecules that don’t flow easily and are hard to ignite. Consequently, fuels like petrol and diesel burn more efficiently and are in higher demand. Thus, cracking breaks down large hydrocarbons into smaller, more useful ones.
This process happens at 600–700°C with a catalyst like silica (SiO₂) or alumina (Al₂O₃). Specifically, the catalyst speeds up the reaction and lowers the energy needed to break chemical bonds. As a result, this creates smaller hydrocarbons, which are easier to refine and use.
For instance, decane (C₁₀H₂₂) can be cracked into octane (C₈H₁₈), used in petrol, and ethene (C₂H₄), used in plastics. Therefore, cracking helps refineries meet demand by converting excess large hydrocarbons into valuable fuels. Additionally, it also produces hydrogen gas, which is used in fertilisers and fuel cells.
There are two main types of cracking. Firstly, catalytic cracking converts heavy hydrocarbons into petrol and diesel using a catalyst. Secondly, steam cracking heats hydrocarbons with steam to produce alkenes like ethene and propene, which are used in the petrochemical industry.
Cracking involves high temperatures and flammable gases, increasing safety risks. Fixed gas detectors monitor for leaks of hydrogen, methane, ethene, and propene. Portable detectors help maintenance teams check high-risk areas. Hydrogen, a byproduct of cracking, is highly flammable and needs constant monitoring. Steam cracking, which operates at extreme heat, also raises the risk of gas leaks.
Gas detection helps prevent fires, explosions, and toxic exposure. It ensures refineries follow safety rules and protect workers. By using advanced monitoring, refineries can run safely and efficiently.
Gas Treatment
Gas treatment removes unwanted substances from raw natural gas. As a result, this process protects pipelines and equipment from corrosion and hydrate formation. Furthermore, it ensures compliance with environmental and market regulations. Without it, proper treatment, natural gas can damage infrastructure, reduce efficiency, and fail to meet safety standards.
The process has several stages, each targeting specific impurities. Initially, the first step removes free liquids and solid particles. Separator units extract water, oil, and solids to prevent blockages in equipment.
Next, acid gas removal, also called gas sweetening, occurs. This step removes hydrogen sulfide (H₂S) and carbon dioxide (CO₂). One common method is amine gas sweetening, which uses solutions like monoethanolamine (MEA) or diethanolamine (DEA) to absorb acid gases. In addition, other techniques include membrane separation and chemical or physical solvents like Selexol and Rectisol.
Subsequently, dehydration follows to remove water vapour and prevent hydrate formation. The two main methods are glycol dehydration and molecular sieve dehydration. Specifically, glycol dehydration uses triethylene glycol (TEG) to absorb moisture, while molecular sieve dehydration relies on zeolite materials for ultra-dry gas.
To stabilise gas for transport, hydrocarbon dew point control removes heavy hydrocarbons. In this process, this step includes condensate removal and cryogenic separation, which extracts ethane and other hydrocarbons. Following this, nitrogen rejection enhances gas heating value using cryogenic distillation or pressure swing adsorption (PSA). Moreover, if mercury is present, activated carbon or molecular sieves capture it to protect equipment.
Gas treatment involves hazardous gases like H₂S, CO₂, methane (CH₄), and volatile organic compounds (VOCs). Consequently, continuous monitoring prevents leaks, exposure risks, and explosions. For instance, during acid gas removal, leaks from amine treatment units or membranes can release toxic gases. To mitigate this, fixed and portable detectors help detect these leaks, protecting workers and equipment.
Dehydration systems can emit VOCs, therefore, requiring monitoring to meet air quality regulations. Similarly, hydrocarbon dew point control and nitrogen rejection pose risks of flammable gas leaks. In addition, methane, ethane, and other hydrocarbons need continuous monitoring to prevent fires and explosions. Lastly, mercury removal also requires detection systems, as mercury vapour leaks can harm health and the environment.
Coking
Coking is a key refinery process that upgrades heavy residual materials from distillation columns into higher-value products. It also produces petroleum coke, a carbon-rich byproduct similar to coal. Petroleum coke is widely used in power generation and industrial applications, particularly in steel and aluminium production.
There are two main coking methods: delayed coking and fluid coking. Both operate at high temperatures above 900°F and slightly elevated pressures to thermally crack the feedstock into valuable products like naphtha and distillates. The remaining solid material forms petroleum coke, classified as either fuel-grade (used as fuel) or anode-grade (further processed for high-purity applications).
Delayed Coking
In delayed coking, the process occurs in large coke drums. Heated feedstock enters these drums, where it cracks over time, forming solid coke. Once full, the coke is removed using hydraulic cutting, where high-pressure water breaks it up for extraction. To maintain continuous operation, feedstock is alternated between multiple drums.
Fluid Coking
Fluid coking is a continuous process where feedstock is introduced into a heated reactor. Here, cracking forms coke particles, which are transferred to a secondary heater. Some coke is burned to generate heat, while the rest is collected for commercial use.
Coking is crucial for refining lower-quality crude oils, which contain more heavy residues. As global demand for fuel grows and crude oil quality declines, coking remains essential for meeting production needs.
Gas Detection in Coking Operations
Coking involves high temperatures, extreme pressures, and hazardous gases, making gas monitoring critical for safety and efficiency.
- Hydrocarbon Gas Leaks – Thermal cracking releases volatile hydrocarbons like methane, ethane, propane, and butane. Leaks in processing units or pipelines can lead to fires or explosions. Fixed and portable gas detectors monitor flammable gas levels to prevent accidents.
- Carbon Monoxide (CO) Monitoring – Fluid coking generates CO during coke combustion. If it accumulates in enclosed areas, it poses a severe poisoning risk. Continuous monitoring ensures worker safety.
- Hydrogen Sulfide (H₂S) Detection – Sulfur compounds in crude oil can produce H₂S, a highly toxic and flammable gas. Fixed and portable detectors help prevent exposure to dangerous concentrations.
- Oxygen Deficiency Risks – Confined spaces in coking units (e.g., coke drums, reactors) can have reduced oxygen levels due to displacement by gases like nitrogen or CO. Oxygen sensors in personal gas monitors are vital for worker protection.
- Particulate and VOC Emissions – Petroleum coke handling and cutting release fine particulates and volatile organic compounds (VOCs). Gas detection and air quality monitoring help ensure compliance with environmental regulations.
Storage Tanks
Storage tanks hold liquids, compressed gases, or thermal mediums for industries like agriculture, manufacturing, energy, and petrochemicals. They safely store substances such as water, chemicals, oil, and gas. Design and functionality vary based on industry needs, with different tanks offering unique safety, environmental, and efficiency benefits.
Types of Storage Tanks
Firstly, fixed-roof tanks are simple and cost-effective, featuring a sealed roof. Industries like petrochemicals, manufacturing, and agriculture commonly use them. Breather valves regulate pressure and vacuum levels.
On the other hand, external floating roof tanks feature a movable roof that floats on the liquid, reducing evaporation and exposure. These tanks prevent product loss, especially in oil and gas operations.
In contrast, internal floating roof tanks combine fixed and floating roof features, which minimises vapour emissions. This design makes them ideal for storing volatile substances.
Moreover, domed external floating roof tanks add a fixed roof that enhances vapour containment and wind resistance. The oil and petrochemical industries widely use these tanks.
Regarding space efficiency, horizontal tanks adapt for both above- and below-ground use. They come equipped with vents and protection against corrosion.
Furthermore, variable vapour space tanks adjust to temperature and pressure changes with lifter roofs or diaphragms, significantly reducing vapour loss in chemical storage.
Additionally, LNG storage tanks consist of double layers designed to store liquefied natural gas at cryogenic temperatures. These tanks play a crucial role in energy storage and transport.
Finally, aboveground storage tanks hold crude oil, diesel, lubricants, and fire water. They are available with fixed or floating roofs.
In contrast, underground storage tanks save space and improve safety. They are common for storing petroleum, chemicals, and water in an oil and gas refinery.
Gas Detection in Storage Tanks
Gas detection ensures safety, compliance, and environmental protection in oil and gas refineries.
- Flammable Gas Detection – Tanks storing methane, propane, or butane require LEL (Lower Explosive Limit) detectors to prevent fire and explosions.
- Oxygen Deficiency Monitoring – Tanks with nitrogen blanketing or displaced oxygen pose suffocation risks. Multi-gas detectors help protect workers.
- Toxic Gas Detection –
- H₂S – Found in crude oil storage, highly toxic at low concentrations.
- CO – Formed from hydrocarbon oxidation, dangerous in poorly ventilated areas.
- NH₃ – Present in chemical and LNG storage, requiring ammonia sensors.
- VOCs – Released from fuels and chemicals, posing health and environmental risks.
- Vapour Recovery & Environmental Monitoring – Gas detectors in vapour recovery units (VRUs) keep emissions within legal limits. Leak detection prevents groundwater contamination.
- Cryogenic Gas Risks in LNG Tanks – Leaks cause rapid gas expansion, leading to asphyxiation and explosion risks. Methane detectors help prevent overpressurisation.
Contact Us
For more information, please get in contact with info@rockallsafety.co.uk or complete the form below or here.