
Top 10 Gas Safety Tips Introduction
Working with gases in the workplace comes with significant safety challenges, as even minor errors can pose serious risks like health hazards, fires, explosions, or environmental damage. Whether dealing with flammable, toxic, or inert gases, it’s vital to follow proper safety protocols to reduce risks and create a safe environment for everyone. From using reliable gas detection tools to ensuring proper storage and handling, these top 10 gas safety tips are designed to help workers stay alert and maintain safety when working with various gases across industries.

1) Know the Hazards of the Gases You’re Using
Each gas has unique risks, such as toxicity, flammability, or asphyxiation, which require specific precautions to handle safely. For example, carbon monoxide is colourless, odourless, and highly toxic, demanding reliable gas detection equipment to ensure worker safety. Flammable gases like propane or methane, on the other hand, can ignite or explode if exposed to sparks or heat, emphasising the need for proper storage and controlled environments.
In the UK, strict regulations govern the handling and use of gases in the workplace to ensure the safety of workers and the public. The primary legislation includes the Health and Safety at Work etc. Act 1974, which establishes a broad framework for maintaining safety in various work settings. This Act applies to all activities, ensuring that employers and employees take all reasonably practicable measures to minimise risks.

2) Ensure Proper Ventilation

3) Use the Right Gas Detection Equipment

4) Wear Appropriate Personal Protective Equipment (PPE)
PPE acts as a barrier that protects the body from harmful exposures, including toxic, flammable, or corrosive gases. This equipment can prevent serious health issues such as respiratory problems, skin irritation, or long-term diseases that can result from inhaling or coming into contact with hazardous substances. The type of PPE needed depends on the specific gases being handled; for example, respiratory protection like gas masks or SCBA (self-contained breathing apparatus) is essential for toxic gas exposure, while chemical-resistant gloves and clothing can protect against skin contact. Proper PPE also helps prevent accidents, supports compliance with safety regulations, and reduces the risk of workplace incidents. Ensuring that all workers are equipped with and properly use PPE boosts safety awareness, enhances productivity, and maintains a safer work environment by mitigating risks associated with gas exposure.

5) Test and Maintain Equipment Regularly
Regular testing ensures that sensors and devices are calibrated correctly, providing accurate readings and minimising the risk of false alarms or missed detections, which could lead to exposure to harmful gases. Maintenance checks help identify any wear and tear, malfunctions, or potential issues that could compromise the equipment’s effectiveness. This proactive approach reduces the risk of equipment failure during critical situations, preventing accidents, health problems, or even fatalities. It also helps meet regulatory requirements and industry safety standards, avoiding legal and financial penalties. Routine maintenance prolongs the lifespan of the equipment, ensuring that it operates efficiently and reliably over time, ultimately creating a safer work environment for all employees.
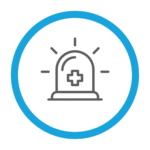
6) Be Prepared for Emergencies
Gas leaks or hazardous gas exposure can happen unexpectedly, and without proper preparation, the risks can escalate quickly, leading to serious injury, health issues, or even fatalities. Emergency preparedness includes having clear plans, training workers on how to respond, and ensuring the availability of emergency equipment like first aid kits and evacuation tools. This readiness allows for quick action to contain or mitigate a situation, such as shutting off gas supplies or evacuating the area safely. It also ensures that workers know how to use gas detection equipment effectively and how to protect themselves using appropriate PPE. Preparedness helps minimise downtime, maintain productivity, and reduce costs associated with accidents and damage control.

7) Conduct Regular Risk Assessments
Gases can pose diverse hazards, such as toxicity, flammability, and oxygen displacement, which could lead to severe accidents or health issues if not properly managed. Risk assessments help identify these dangers, evaluate their potential impact, and implement effective control measures to mitigate risks. They also ensure compliance with workplace safety regulations, such as COSHH in the UK, protecting employees and avoiding legal repercussions. Regular assessments allow for updates to procedures and equipment, ensuring they remain effective in evolving workplace conditions.

8) Do Not Over-Tighten Valves or Regulators
Valves and regulators are precision-engineered to create a proper seal with the correct amount of force; over-tightening may strip threads, distort seals, or crack fittings, potentially resulting in gas leaks. Gas leaks can lead to harmful exposure, fire risks, or oxygen displacement, depending on the gas involved. Additionally, damaged components may require costly repairs or replacements and could lead to downtime. Following manufacturer guidelines ensures optimal performance and workplace safety.

9) Purge Lines and Equipment Safely
Purging lines and equipment safely is crucial when dealing with gases in the workplace to prevent contamination, ensure system integrity, and avoid hazardous reactions. Residual gases in equipment can mix with incoming gases, leading to unintended chemical reactions, fire, or explosion risks. For example, purging flammable or toxic gases without proper care can endanger workers and compromise air quality. Safe purging ensures that lines and equipment are free from unwanted residues, maintaining the accuracy of operations and protecting both personnel and the environment. It also minimises downtime and helps meet regulatory standards for safety and compliance.

10) Never Rely on Smell Alone
Gases like carbon monoxide (CO) and nitrogen are entirely odourless but can be deadly, while some odorous gases, such as hydrogen sulphide (H₂S), can dull your sense of smell over time, creating a false sense of safety. Additionally, relying on smell doesn’t provide quantitative information about gas concentration levels, making it an unreliable method for ensuring safety. Using appropriate gas detection equipment is essential for accurately identifying and monitoring gas hazards.